Machining and industrial processes need to be optimized to meet the high demands of production while minimizing operational expenses to compete in today's competitive market. One vital system used in various applications is the filter press, which plays a key role in liquid-solids separation and sludge dewatering. Over time, existing filter press equipment may suffer from decreased efficiency due to age and wear. This can lead to maintenance issues and subpar production levels. In this article, we will discuss the importance of filter press upgrades for industrial efficiency.
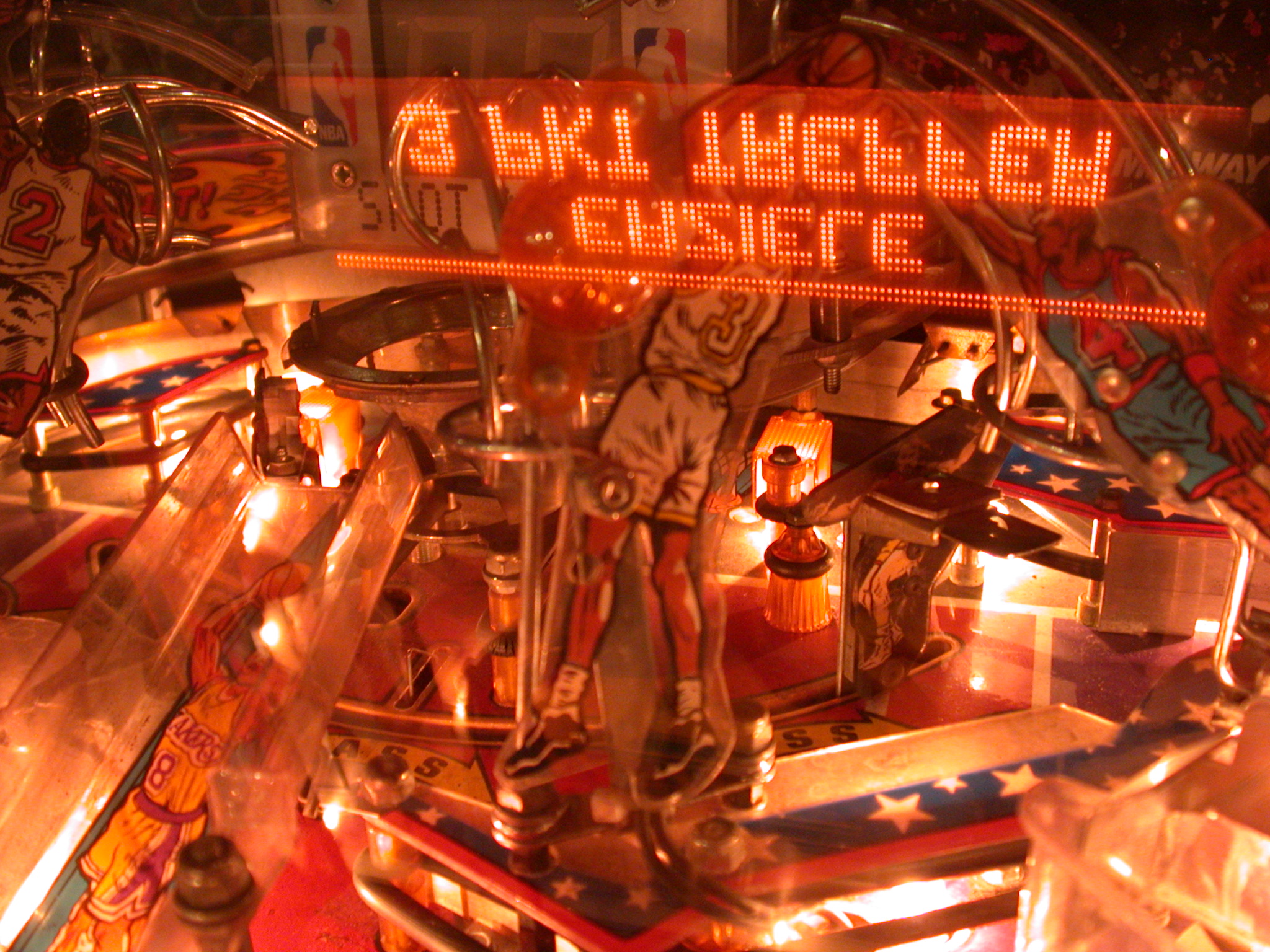
Filter press upgrades are critical for maintaining high production levels and efficient industrial operations. As machines age, they may develop problems such as increased energy consumption, inefficient dewatering, and reduced pulp concentration in the final cake. It can be challenging to remove contaminants during the dewatering process, resulting in lower-quality end products. Moreover, inefficient equipment can result in increased costs due to higher energy consumption and potential equipment breakdowns.
Upgrading the filter press to a modern, more efficient model can greatly benefit industrial operations by enhancing performance and productivity. Advances in technology have resulted in more advanced filter press designs that incorporate numerous features aimed at enhancing performance and productivity. Some key benefits of upgrading include improved dewatering capabilities, increased capacity, reduced energy consumption, and automated operation for enhanced safety and minimal human intervention.
Another significant advantage of upgrading to modern filter presses is lower energy consumption and improved environmental sustainability. Older filter presses often consume a lot of energy, leading to increased operational costs. Newer models, however, are designed with energy efficiency in mind and utilize more efficient motors and mechanisms, resulting in lower energy expenditure.
Furthermore, they often feature advanced controls and sensors that help streamline the operation and minimize downtime.
When planning to upgrade a filter press, industrial operators must consider various factors, including the type of process being used, the type of sludge or contaminated materials being processed, and the desired level of efficiency. Consultation with experienced industrial experts is required to assess current operation, identify areas for improvement, and determine the best upgrade path.
In conclusion, hydraulic filter press manufacturers press upgrades are a critical component in maintaining high industrial efficiency. Upgrading to modern, energy-efficient filter presses not only improves dewatering capabilities and reduces operational costs but also ensures production continuity and minimizes the possibility of equipment failures. Proper evaluation of current operation and consulting with experts can help determine the most suitable filter press upgrade for each industrial operation, resulting in improved efficiency, productivity, and overall competitiveness.